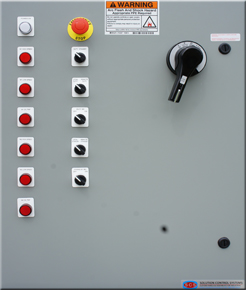
What is a Motor Starter?
A motor starter is a crucial electrical component designed to initiate, control, and safeguard electric motors. During the startup process, motors draw high current levels, potentially damaging both the motor and the connected electrical system. A motor starter helps prevent this by gradually supplying power to the motor, thereby reducing the initial current spike and allowing for a smooth, controlled startup. It typically includes contactors that manage the motor’s electrical connection, overload protection to guard against excessive current, and a control circuit to oversee the motor’s operation. Motor starters are widely used across various industries, including manufacturing and transportation, ensuring reliable and secure motor operation.
Why is it necessary to connect a Starter to Electrical Motors?
Motor starters play a critical role for several reasons:
- They limit the high inrush current during motor startup, protecting the motor and the electrical system from potential damage. The starters extend the motor’s lifespan and reduce maintenance costs.
- Motor starters enable a smoother startup, minimizing mechanical strain on connected equipment and avoiding abrupt movements.
- They offer overload protection by automatically disconnecting the motor if excessive currents are detected, preventing possible motor damage. Certain starters include reversing functionality for applications requiring the motor to run in both directions. Overall, motor starters enhance motor operations’ efficiency, safety, and control.
How does an industrial Motor Starter work?
An industrial motor starter operates through a combination of electromechanical and electronic components. When the start button is pressed, the control circuit activates the coil of the main contactor, which closes its main contacts, connecting the motor to the power supply. Throughout the operation, overload relays monitor the motor’s current to ensure it stays within safe limits. If the current exceeds these limits, the overload relay trips, cutting power to the motor and preventing damage. Pressing the stop button interrupts the control circuit, de-energizing the main contactor and stopping the motor. Additionally, motor starters use auxiliary interlocks to manage proper sequencing and ensure safe operation.
Types of Motor Starters:
• High torque starters
• Low torque starters
• Slow starting speed starters
• High starting speed starters
• Custom combinations or time-based variations depending on the load requirements.
High Torque Motors:
Advantages |
Disadvantages |
|
|
|
|
|
Low Torque Motors:
Advantages |
Disadvantages |
|
|
|
|
|
Slow Starting Speed Motors:
Advantages |
Disadvantages |
|
|
|
|
|
High Starting Speed Motors:
Advantages |
Disadvantages |
|
|
|
|
|
|
Motor ElementsA motor starter setup includes an incoming power connection (single or three-phase) linked to a protective device such as a fuse block or circuit breaker, sometimes equipped with a locking mechanism. It also features contactor switchgear paired with an overload relay, either integrated or separately connected, and power cables that lead directly to the field motor or intermediate terminal blocks. Variations in the setup may include a soft starter or Variable Frequency Drive (VFD) positioned after the contactor for smoother motor control, providing a range of options to suit different motor requirements. The control elements play a crucial role in managing the motor. These consist of selector switches like Auto/Manual and Local/Remote modes, with push buttons for Motor Start/Stop and pilot indicators to display motor status. In automated systems, the motor can be controlled by a programmable logic controller (PLC) or another control device. Depending on the location of the control system (PLC or motor control relay), the motor starter panel may also include wiring for signals related to motor monitoring, such as motor temperature, vibration, overload conditions, operation status, forward/reverse motion, and feedback from connected equipment. Motor starter panels are designed to integrate various starter types and include all necessary isolation, safety, protection, and control features. These panels are custom-engineered based on specific motor requirements and are almost ready for operation upon basic installation. Note: Typical motor starters available on the market include Direct-On-Line Starters, Star-Delta Starters, Reversing Starters, Soft Starters, and VFD Starters. |
Available Options:
- 4X stainless steel or fibreglass enclosures
- Floor mount kits
- Inner Door for control access
- NEMA style contactors
- Electronic overload protection
- Multi-motor control capability
- Duplex pump control
- Automatic transfer control
- Multi-winding/speed motor control
- Enclosure Heaters
- Single-phase motor applications
- Custom control configurations
- Class 1 Div1 or two starters in explosion-proof enclosures and purge panels.