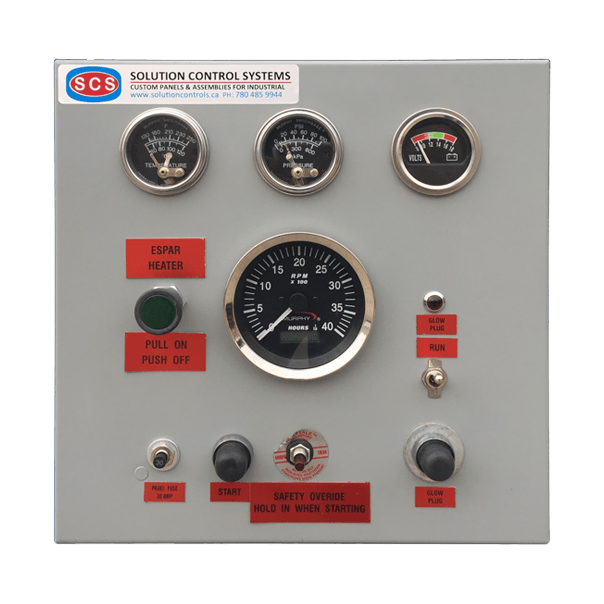
Instrumentation Panels & Racks
Instrument racks and panels are engineered custom built solutions to accommodate, organize instruments for the purposes of detection, measurement, indication, monitoring, protection, control and management of process/ energy in action.
The panels/racks are designed based on the type of energy and dynamics associated. Each rack or panel, irrespective of the type of energy involved, will have controls in minimum such as input engage, pass through, bypass, isolation, and shutdown. The additional features would include, indication, and communication.
The physical form of instruments could be valves, gauges, electrical, electronic meters, with functional mediums such as electrical, mechanical, gas, liquid, pneumatic, hydraulic etc.
Modern industry uses instruments for management of various parameters such as Electrical (Voltage/ Current/ Power), Process, kinetic, potential, kinematic, physical, chemical, biological, analytical (temperature, pressure, flow, velocity, acceleration, density, viscosity, level, mass, volume compositions), Electromagnetic, Telemetric, Geotechnical, Nuclear, Etc.
Important electrical design considerations in instrument panels are the separation of instrument grounding from electrical system ground. This is an important safety and performance requirement in dealing with electrical and signal noise issues. The instrument panels need to placed away from high switching noise producing elements such as VFDs, Motors, and pumps. Failing to do this would result in switching noises affecting the measurement.
Instrument signal communication would involve direct wiring of 4-20mA or DC voltage, and communication systems named on RS232/485/ HART/ Modbus, Profibus, Foundation fieldbus, Devicenet, Controlnet, Ethernet, DNP3, ZIgbee protocols based on the type of control hardware and topology chosen.
The instrument selection would include safety integrity level specification based on a HAZOP analysis.